Why Scaling Up Is No Longer the Only Strategy
To gain access to all Ideas for Leaders content please Log In Here or if you are not already registered then Register Here.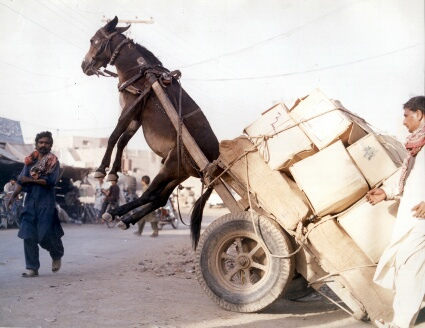
Traditionally, industrial production has moved in only one direction: from small to large. ‘Scaling up’ was the best way to maximize productivity and lower per-unit costs. A fleet of 100 ten-ton dump trucks requires more drivers than a fleet of 10 hundred-ton dump trucks. But automation and communication technology has evolved to the point where a large number of small units may be cheaper, better and more efficient than a small number of large units.
To read the full text on this Idea you will need to log-in or register with the Ideas for Leaders site. Please click here to log-in and here to register for the first time.
If you are a member of one of our Sustainable Leadership Communities you can log-in using your SLC log-in details, with your email prefixed by the community group you are in. eg: uk.jane.fraser@abcgroup.com
Ideas for Leaders is a free-to-access site. If you enjoy our content and find it valuable, please consider subscribing to our Developing Leaders Quarterly publication, this presents academic, business and consultant perspectives on leadership issues either as a digital subscription, or better still in a beautifully produced, small volume delivered to your desk four times a year.
For the less than the price of a coffee a week you can read over 650 summaries of research that cost universities over $1 billion to produce.
Use our Ideas to:
Speak to us on how else you can leverage this content to benefit your organization. info@ideasforleaders.com