Is Your Supply Chain Prepared for the Unexpected?
To gain access to all Ideas for Leaders content please Log In Here or if you are not already registered then Register Here.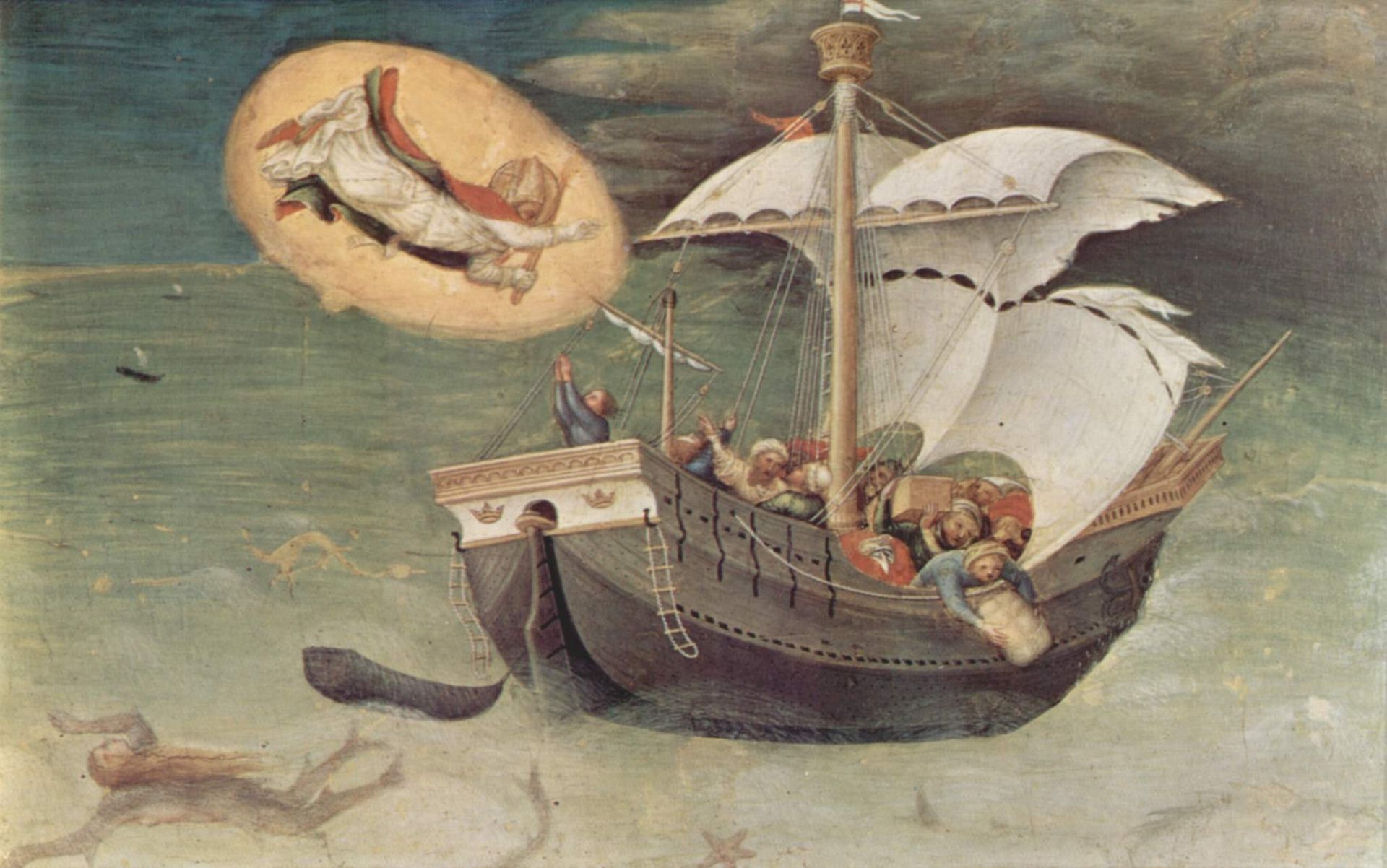
Supply chain management is a delicate balancing act in these unpredictable times – on the one hand, there is pressure to keep the supply chain as cost efficient as possible, while on the other, it needs to be flexible and resilient in the face of unforeseen events. How do leaders proactively manage the risk of disruption?
To read the full text on this Idea you will need to log-in or register with the Ideas for Leaders site. Please click here to log-in and here to register for the first time.
If you are a member of one of our Sustainable Leadership Communities you can log-in using your SLC log-in details, with your email prefixed by the community group you are in. eg: uk.jane.fraser@abcgroup.com
Ideas for Leaders is a free-to-access site. If you enjoy our content and find it valuable, please consider subscribing to our Developing Leaders Quarterly publication, this presents academic, business and consultant perspectives on leadership issues either as a digital subscription, or better still in a beautifully produced, small volume delivered to your desk four times a year.
For the less than the price of a coffee a week you can read over 650 summaries of research that cost universities over $1 billion to produce.
Use our Ideas to:
Speak to us on how else you can leverage this content to benefit your organization. info@ideasforleaders.com